Protobind® KW
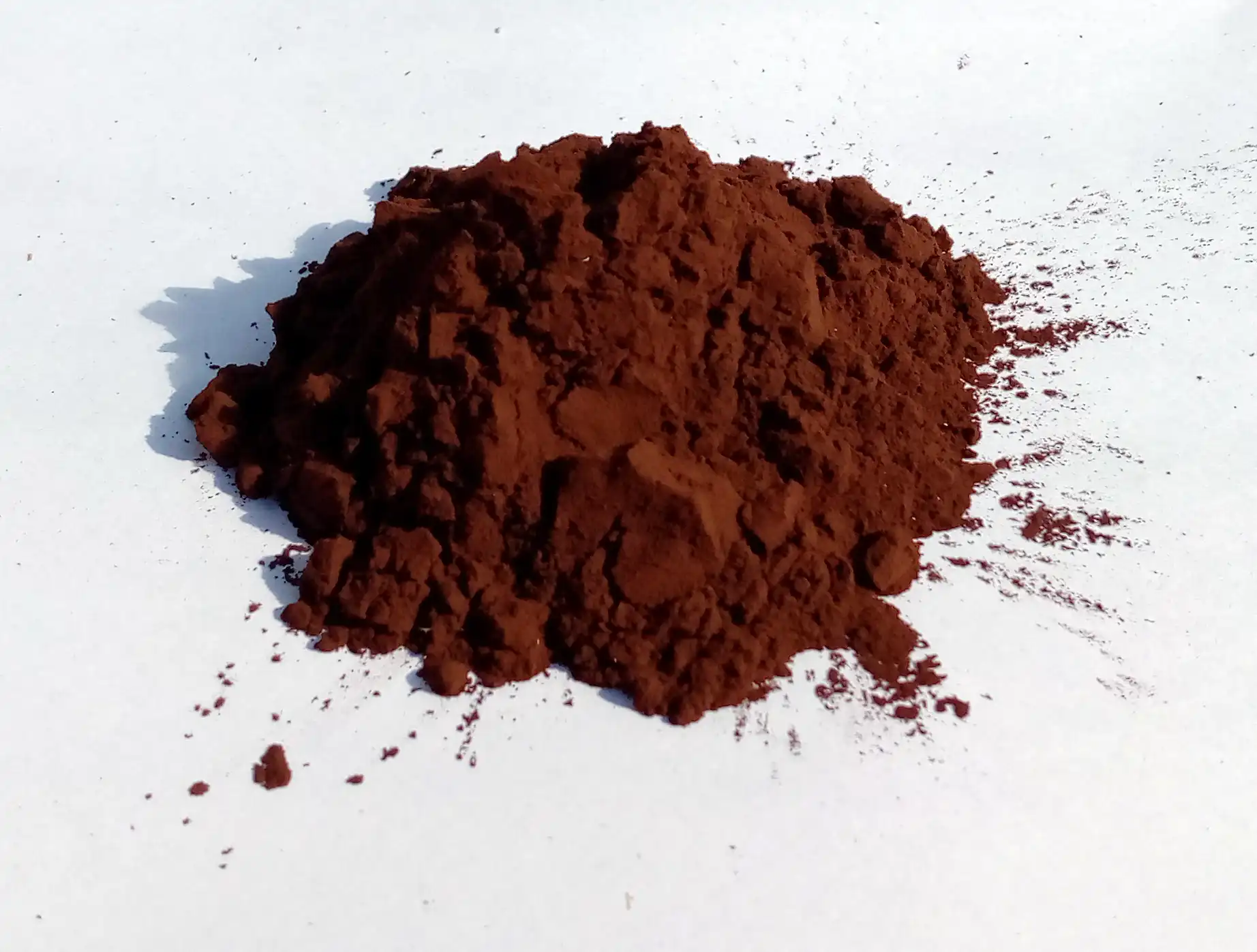
Protobind KW is our speciality product with proven capability to be used in PF resin manufacturing process. This product, as a natural polyphenolic material obtained from woody plants, offers a bio-based alternative to fossil-based materials such as phenol. Our product can be used as a partial substitute for phenol used in PF resin production. The replacement degree can be flexible, depending on the layout and design of the available production process to produce lignin-based PF resin. However, thanks to intensive research work, plenty of modification methods are available to apply to ease and optimise the processes.
Along with the production of lignin in the site, our R&D laboratory has investigated the impact of partial phenol replacement by Protobind KW in PF resin on respected characteristics. The detailed investigation has been on the kinetics of viscosity gain during resin cooking, on its curing characteristics, physical properties, and mechanical bonding attributes. This database along with available supportive publications would provide our clients with a massive knowledge to conduct their own process using the bio-based lignin Protobind KW.
Download Datasheet for Protobind KWProtobind - KW - LABORATORY RESULTS
The utilisation of lignin in phenolic resin results in a significant acceleration in polymerization rate during resin synthesis, and consequently a cost-effective impact with economic benefit. The graph below illustrates the fact for our laboratory-made resins. The 20%Lignin-PF and 40%Lignin-PF contain 20 and 40% Protobind KW respectively, that have been compared with PF resin containing no lignin.Differential Scanning Calorimetry (DSC) is a recommenced technique to evaluate the chemical behaviour of polymeric materials.
According to DSC testing, lignin is to demand more energy to form the crosslinked structure of cured resin in end-product. This additional energy demand is due to steric effects of lignin. DSC graphs below have been obtained for our laboratory-made resins containing Protobind KW, which indicates an increase for curing temperature for lignin-based resins. However, this additional energy demand could be compensated by the economic benefit coming from the shorter cooking time during resin synthesis described before.
According to this test for our laboratory-made resins, proceeding with a lignin substitution degree up to 20%, the adhesive bonding performance is preserved with a slight reduction. However, up to 40% substitution there is an evident reduction which is compensable by means of known methods. This observation is displayed in the graph on the right.
As a matter of fact, there are modification methods to improve the possible loss. Fillers, crosslinkers and hardeners are known for PF resin manufacturers to boost adhesion strength. The impact of using a type of fillers has been shown in the graph on the right as an example. Furthermore, some improvements could be implemented into the resin-making instructions and processes to ease lignin integration into the system.
For a Free Consultation, Call
We are just a call away to answer all your queries.
Contact Us
Location:
Registered & Corporate Office
W1A, FIRST FLOOR, TOWER A,
GODREJ ETERNIA, PLOT NO. 70, INDUSTRIAL AREA,
Phase 1,
Chandigarh - 160 002